

The hardest thing about surfacing is truly not one single workflow or process that is “correct”. Explore different solutions and techniques. Don’t be afraid to make copies at various points in the process. Remember that you’re working with a digital file. This method can save a lot of time in comparison to the traditional process of trimming, patching and stitching every area of the model. The Boundary Fill command will fill the object, trim the excess parts, and leave us with a solid body all with one single feature. Create surfaces on all sides of the object so there are no openings. The Boundary Fill command will save you a lot of time. The order of how you trim surfaces will sometimes affect the outcome, especially when you have many surfaces that need trimming. You’ll need to think through your trimming process before attempting to use it. The trim tool will let you trim away all the excess parts, making sure your corners and adjacent geometry don’t end up with unintentional openings. You’ll want to extrude surfaces well past their desired stopping point. This goes hand-in-hand with best practice #2.
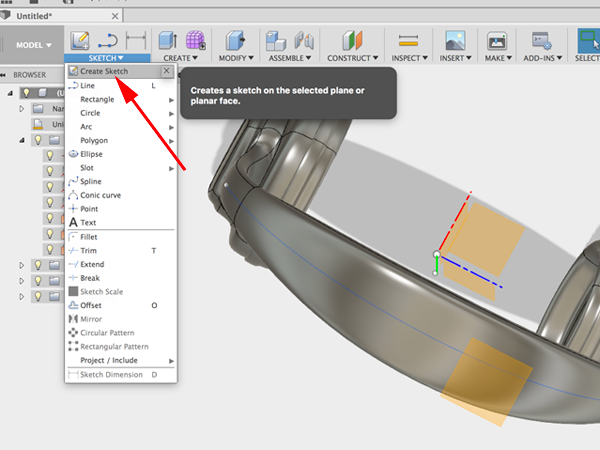
The Trim tool is one of the most used surface tools. This allows you to check the surface geometry without any obstructions. It’s also a good idea to hide all of your sketches, reference images, and construction planes regularly. The key thing is to make sure you’re not using one of the wireframe settings. However, either of the shaded options that show edges will work. I prefer the “shaded with visible edges only” option. #4 Shaded Visibilityīecause surface modeling is all about creating smooth geometry, you’re going to want to make sure you’re modeling with one of the “shaded” visibility settings. Don’t be afraid to suppress the later features in your timeline while you readjust the initial surfaces. You’ll find that it will take some back and forth to refine the model. For example, with the steam iron demo, I started with the outer surface without worrying about the opening for the handle. Try to focus completely on the furthermost outside geometry first.Īfter you’ve created the rough shape you can start to work your way inward, creating the details of the model. It’s easy to get caught up in the details when starting a new surface model. Surface modeling is exactly what it sounds like – you’re modeling the outer surface. This helps ensure that adjacent surfaces don’t have opening or voids that would prohibit the model from becoming a water-tight solid body. Surfaces should be cleaned up with the trim tool. This helps ensure that your surface extrusions collide with adjacent surfaces. Your sketch geometry can (and should) run past one another. Surfacing requires different sketch geometry than solid modeling.
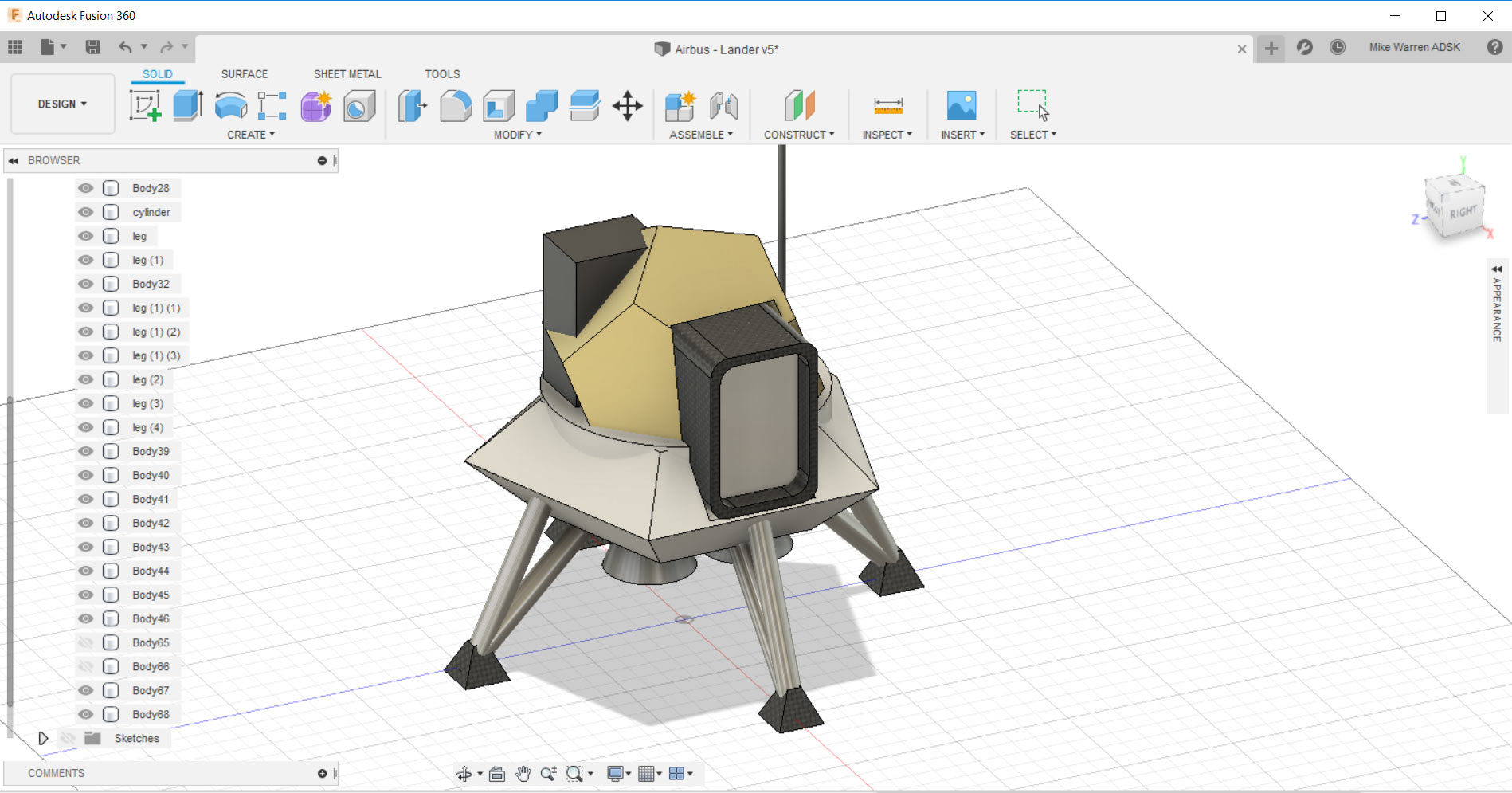
Try to keep the adjustment of spline handles to a minimum and use constraints when possible. You’ll also find the more you tweak spline handles the more you’ll create bad curvature.
Fusion 360 tutorial patch how to#
If that is the case then the focus should be on how to use the fewest amount of control points. Sometimes it’s impossible to not use splines. Try using arcs or conic curves instead of splines. Splines often result in wavy geometry that isn’t ideal.
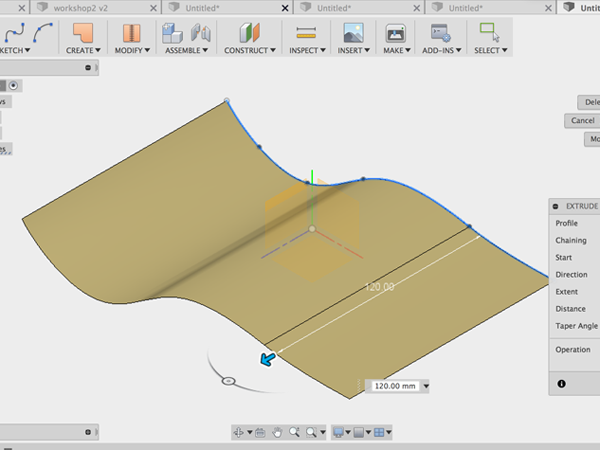
You’ll want to avoid spines as much as possible. The focus of surface modeling is to create smooth exterior surfaces. 7 Surface Modeling Best Practices #1 Avoid Splines I’ll also be walking you through step-by-step some of these core workflows. Instead of explaining every little detail, I’m going to show you some surface modeling best practices, so you can start to consider how they could be applied in your own projects. By the end of this tutorial, you’ll know some core surface modeling techniques to use while working in Fusion 360.
